Solenoid-operated, avance rápido y regulado control de caudal ensamblaje
Function
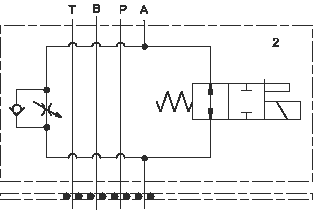
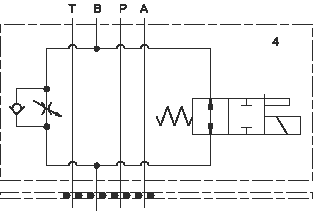
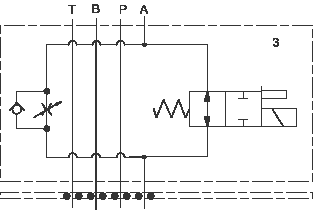
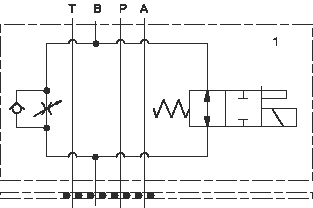
This assembly consists of needle valve, which is a fully-adjustable orifice used to regulate flow with a reverse-flow check. It is not pressure-compensated. It may be used as a flow control or as a shutoff valve. The rapid or feed rate is selected by a solenoid operated (normally open or closed) 2-way, 2-position valve.
- The sharp-edged orifice design minimizes flow variations due to viscosity changes.
- Because needle valves are non-compensating devices, the fixed orifice size will regulate flow through the valve in proportion to the square root of the pressure differential across ports 1 and 2.
- Now available with FLeX Series solenoid valves. See CONFIGURATION section, SOLENOID DESIGNATION to specify.
Body Type | aplilablesaplilables |
Interface | ISO 03ISO 03 |
Capacity | 12 gpm45 L/min. |
Body Features | alimentación regulada en A o B, descarga regulada en A o Balimentación regulada en A o B, descarga regulada en A o B |
Stack Height | 1.75 in.44,5 mm |
Seal Plate Included (see notes) | YesYes |
Control Flow Range | 0 - 7 gpm0 - 7 gpm |
Direct-acting valves are used to prevent over pressure, and pilot-operated valves are used to regulate pressure. If you are unsure, use a direct-acting valve. Sun's direct acting valves are very fast, dirt tolerant, stable, and robust. Sun's pilot-operated valves are moderately fast, they have a low pressure rise vs. flow curve, and they are easy to adjust.
There are exactly 250 Sun drops in a cubic inch or 15 in a cc.
Reasons to anodize:
- To increase corrosion resistance. Sun uses 6061-T651 aluminum. It is one of the most corrosion resistant aluminum alloys there is. Whether or not anodizing improves the corrosion resistance of 6061 aluminum is debatable. We have yet to have a manifold returned because of corrosion.
- Appearance (color). The 2 colors that would appeal to Sun would be blue or black. Unfortunately these are the colors that are hardest to do consistently.
- To provide a hard wear surface. Sun does not make parts-in-body valves. The manifold is just plumbing. We don't need a wear surface.
- Because everyone else does it. Bad reason.
Reasons to not anodize:
- Cost. It's another process.
- Logistics. When you make tens of thousands of manifolds a month and you anodize hundreds, it's a problem. Consistency. See above.
- Stamping. After a body is anodized you cannot do any more stamping without making a mess.
Inspection. Have you ever tried to look for burrs in a black anodized body? It's the old blackboard factory at night scenario. - Torque. You will experience an increase in breakaway torque when removing items from an anodized manifold.
- Fatigue life. This is the best reason to not anodize. Fatigue failure is a very complex phenomenon. What it takes to initiate a crack is difficult to predict. What it takes to propagate a crack is readily defined. Anodizing produces a very thin, very hard, and very brittle surface on aluminum. The first time you pressurize an anodized aluminum manifold you have initiated fatigue cracks. Whether or not the stress is enough to propagate the cracks is a matter of pressure and manifold geometry. Anodizing an aluminum manifold grossly reduces the fatigue life by anywhere from 20% to 50%.
- Stack height value in technical data table includes seal retainer plate.
- For detailed information regarding the cartridges contained in this assembly, click on the models codes shown in the Included Components tab.
- Important: Carefully consider the maximum system pressure. The pressure rating of the manifold is dependent on the manifold material, with the port type/size a secondary consideration. Manifolds constructed of aluminum are not rated for pressures higher than 3000 psi (210 bar), regardless of the port type/size specified.
- Putting Sun at the heart of hydraulic regenerative braking systems
- NUEVO: Soluciones de control de flujo con prioridad ajustable
- Conjuntos integrados: Soluciones que hacen crecer su reputación
- Nuevas soluciones rápidas de avance y alimentación
No coil selected.